Table Of Contents
Cold rooms are essential for businesses that require controlled-temperature environments to store perishable goods such as food, pharmaceuticals, and other temperature-sensitive products.
Constructing a cold room requires careful planning and selecting appropriate materials to ensure optimal performance and energy efficiency. This article will explore the materials needed to build a cold room and discuss their importance in maintaining the preferred temperature and humidity levels. Let's dive in!
Planning and designing
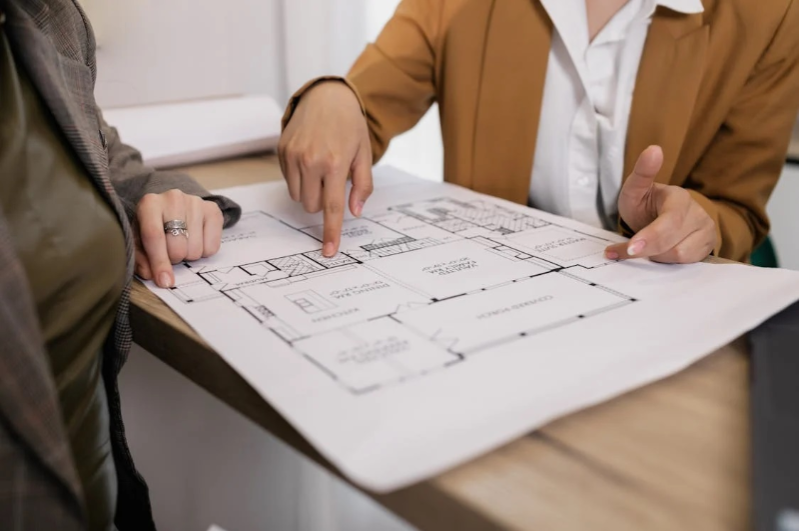
It is crucial to assess the space requirements and determine the insulation needs based on the facility's intended use before constructing a cold room. Factors such as the cold room's size, required temperature range, and access frequency should be considered during the planning phase. Additionally, the type of temperature control systems, such as refrigeration units or cooling systems, must be chosen based on the cold room's specific requirements.
Structural materials
The structural integrity of a cold room is essential for maintaining consistent temperatures and preventing heat transfer from the external environment. The cold room's walls, flooring, and ceiling should be constructed using durable and insulating materials to minimise heat loss and ensure energy efficiency. Common materials used for cold room construction include insulated panels, reinforced concrete, and high-density polyethene (HDPE) sheets.
Insulation materials
Insulation is a critical component of a cold room as it helps to prevent heat transfer and maintain the desired temperature inside the facility. Various insulation materials, including expanded polystyrene (EPS), polyurethane foam, and mineral wool, can be used.
The choice of insulation material relies on factors such as thermal conductivity, moisture resistance, and fire safety requirements. Proper insulation installation is essential to minimise thermal bridging and ensure maximum energy efficiency.
Vapour barrier and sealants
The significance of vapour barriers and sealants in constructing a cold room cannot be overstated. These components play crucial roles in maintaining the integrity of the cold room's insulation and preventing moisture infiltration, which can compromise the insulation's effectiveness and lead to mould growth and structural damage.
A vapour barrier is typically a thin layer of material installed on the warm side of the insulation to inhibit the movement of moisture vapour into the insulation and building envelope. Common materials used for vapour barriers include polyethene sheets, foil-faced insulation, and specialised vapour barrier membranes.
The vapour barrier should be installed carefully to ensure a continuous and tight seal, minimising the risk of condensation buildup within the insulation. In addition to vapour barriers, sealants seal gaps, joints, and penetrations in the cold room's structure, ensuring an airtight and watertight seal.
Silicone sealants, polyurethane foam sealants, and specialised cold room sealants are commonly used. Proper sealant application prevents air leakage and maintains the desired temperature inside the cold room.
Refrigeration system components
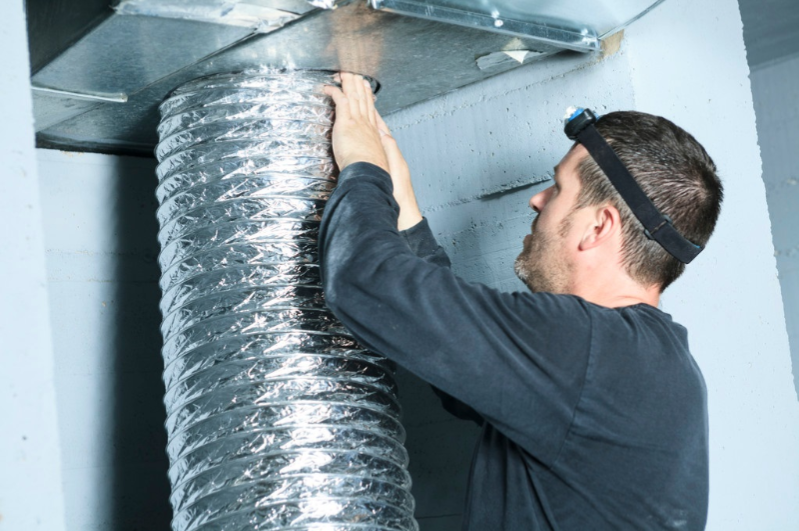
The refrigeration system is the heart of any cold room. It holds the desired temperature and humidity levels to preserve the stored goods. Understanding the various components of the refrigeration system is essential for designing and building an efficient and reliable cold room.
- Compressors: Compressors compress the refrigerant gas, increasing its pressure and temperature before it enters the condenser. Typical compressors in cold room applications include reciprocating, scroll, and rotary compressors. The choice of compressor depends on factors such as cooling capability, energy efficiency, and noise levels.
- Evaporators: Evaporators are heat exchangers that facilitate heat transfer from the cold room to the refrigerant gas, causing the refrigerant to evaporate and absorb heat from the surrounding environment. Evaporators come in various configurations, including finned coil evaporators, shell-and-tube evaporators, and plate heat exchangers. Proper selection and installation of evaporators are critical for achieving efficient cooling performance and uniform temperature distribution within the cold room.
- Condensers: Condensers reject heat from the refrigerant gas to the external environment, causing the gas to condense into a liquid state. Air-cooled, water-cooled, and evaporative condensers are common types used in refrigeration systems. The choice of condenser depends on factors such as space constraints, ambient temperature conditions, and energy efficiency requirements.
Note: Understanding the functions and characteristics of compressors, evaporators, and condensers is essential for selecting the appropriate refrigeration system components for a cold room application.
Doors and access points
The design and selection of doors and access points for a cold room are critical considerations that impact energy efficiency, temperature control, and ease of operation. Different types of doors are available, each offering unique features and benefits suited to specific cold room applications.
- Hinged doors: Hinged doors are the most ordinary type of door used in cold rooms. They offer ease of access and a tight seal when closed. These doors typically feature insulated panels and gaskets to minimise heat transfer and prevent air leakage. Hinged doors can be equipped with various locking mechanisms and accessories to enhance security and functionality.
- Sliding doors: Sliding doors are ideal for cold rooms with limited space or requiring frequent access. These doors slide horizontally along tracks mounted on the floor and ceiling, allowing smooth and efficient operation. Sliding doors can be configured with manual or automated opening mechanisms, depending on the application requirements.
- High-speed doors: High-speed doors are invented for rapid opening and closing, minimising temperature fluctuations and energy loss during frequent entry and exit. These doors feature insulated panels and high-speed operation mechanisms, making them suitable for cold rooms in high-traffic areas such as warehouses and distribution centres. High-speed doors can significantly improve operational efficiency and energy savings in cold room environments.
When selecting doors and access points for a cold room, consider factors such as door size, insulation properties, sealing mechanisms, and access control features. Proper installation and maintenance of doors are essential to ensure optimal performance and longevity.
By incorporating energy-efficient LED lighting fixtures, enclosed fixtures, and motion sensor controls, cold room operators can optimise lighting performance, minimise energy consumption, and create a safe and comfortable working environment for personnel.
Lighting
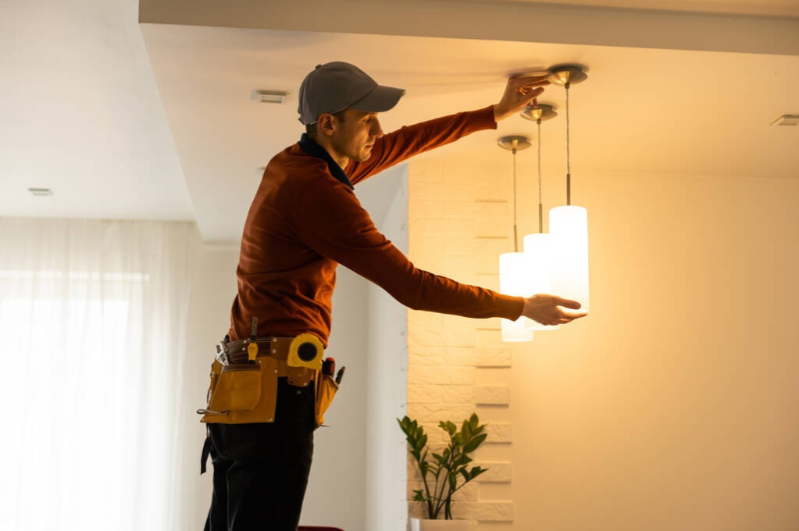
Adequate lighting ensures visibility, safety, and productivity in a cold room. Proper lighting design and selection can also contribute to energy efficiency and minimise heat gain, helping to maintain stable temperature conditions within the cold room.
- LED lighting: LED (light-emitting diode) lighting fixtures are preferred for cold room applications due to their energy efficiency, durability, and superior light quality. Compared to traditional lighting technologies, LED fixtures produce minimal heat output, reducing the risk of heat gain and maintaining a cooler environment inside the cold room. Additionally, LED lighting offers long service life and low maintenance requirements, making it cost-effective and environmentally friendly.
- Enclosed fixtures: Enclosed lighting fixtures are recommended for cold room environments to protect against moisture ingress and contamination. Sealed or gasketed fixtures prevent water vapour and condensation from compromising the electrical components and light sources, ensuring safe and reliable operation in cold and damp conditions. Enclosed fixtures also help maintain hygiene standards by preventing dust, dirt, and debris accumulation inside the cold room.
- Motion sensor controls: Motion sensor controls can be integrated into lighting systems to turn lights on or off automatically based on occupancy detection. This feature helps reduce energy consumption and operating costs by ensuring that lights are only activated when needed. Motion sensor controls are particularly beneficial in cold rooms with intermittent usage or areas with low foot traffic, where lights may be inadvertently left on for extended periods.
Monitoring and control systems
Monitoring and control systems are crucial in ensuring proper operation, efficiency, and safety of cold room facilities. These systems allow real-time monitoring of temperature, humidity, and other environmental conditions, allowing operators to identify possible issues and take corrective action before they escalate into problems.
- Temperature monitoring devices: Temperature sensors and probes are installed throughout the cold room to measure and monitor ambient temperature levels. These devices provide accurate and reliable temperature readings, allowing operators to preserve precise control over the cold room environment and ensure compliance with temperature-sensitive storage requirements. Advanced temperature monitoring systems may feature wireless connectivity, data logging capabilities, and alarm notifications to alert operators of temperature deviations or equipment malfunctions.
- Alarm systems: Alarm systems are essential for alerting personnel to critical events or conditions that require immediate attention. In cold room environments, alarms may be triggered by temperature deviations, equipment failures, power outages, or security breaches. Audible alarms, visual indicators, and remote notification capabilities are commonly used to notify operators of alarm conditions and prompt timely responses to prevent product loss or equipment damage.
- Remote access capabilities: Remote monitoring and control capabilities allow operators to access and manage cold room systems from anywhere with an internet connection. Cloud-based monitoring platforms and mobile applications enable remote monitoring of temperature, alarm status, and equipment performance, providing real-time insights and actionable data for informed decision-making. Remote access capabilities empower operators to respond promptly to changing conditions, troubleshoot issues remotely, and optimise cold room operations for maximum efficiency and reliability.
Note: Cold room operators can enhance operational efficiency, minimise downtime, and ensure product quality and safety by implementing advanced monitoring and control systems.
Maintenance and upkeep
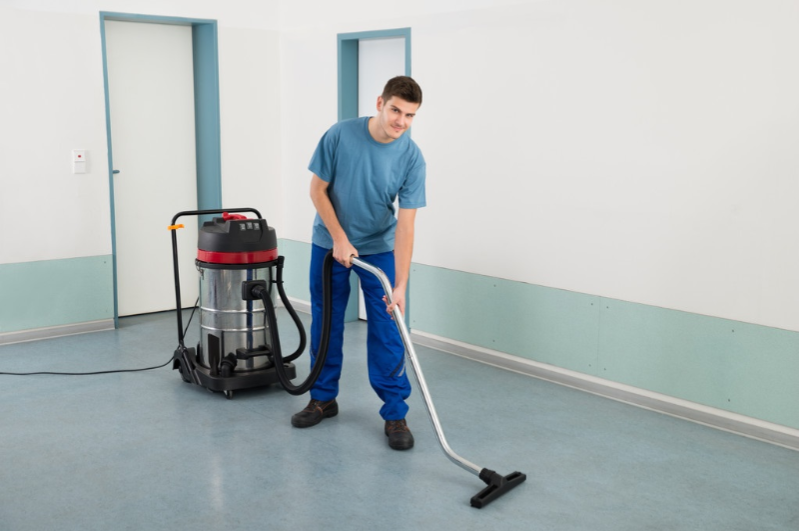
Regular upkeep and care are essential for preserving the performance, efficiency, and longevity of cold room facilities. Proper maintenance practices help identify and address potential problems before they escalate into pricey repairs or equipment failures, ensuring uninterrupted operation and optimal product storage conditions.
- Regular inspections: Scheduled inspections should be conducted to assess the condition of cold room components, including insulation, doors, refrigeration equipment, and lighting fixtures. Inspections help determine signs of wear and tear, damage, or malfunction that may compromise the integrity or performance of the cold room. Visual inspections, equipment checks, and performance testing should be performed by qualified personnel to identify and address maintenance needs promptly.
- Cleaning procedures: Routine cleaning is essential for preventing the buildup of dirt, dust, mould, and contaminants inside the cold room. Floors, walls, ceilings, shelving, and equipment should be cleaned regularly using approved cleaning agents and sanitisers to maintain hygiene standards and prevent microbial growth. Condenser coils, evaporator fins, and air filters should be inspected and cleaned to ensure optimal airflow and refrigeration efficiency.
- Troubleshooting common issues: Cold room operators should be familiar with common issues and troubleshooting procedures to address minor problems and prevent downtime. Common issues such as temperature fluctuations, frost buildup, condensation, and equipment malfunctions may arise due to improper insulation, refrigerant leaks, or electrical faults. Operators should be trained to identify symptoms, diagnose root causes, and implement corrective actions to restore regular operation and prevent the recurrence of issues.
Note: By implementing a proactive maintenance program that includes regular inspections, cleaning procedures, and troubleshooting protocols, cold room operators can maximise equipment reliability, minimise downtime, and ensure consistent performance and product quality.
Compliance and regulations
Compliance with building codes, regulations, and industry standards is critical for ensuring cold room facilities' safety, reliability, and legality. Regulatory requirements may vary depending on facility location, size, occupancy, and intended use.
Cold room operators must familiarise themselves with relevant regulations and standards and ensure compliance with applicable requirements to avoid fines, penalties, and legal liabilities.
- Building codes and standards: Building codes govern the design, construction, and operation of cold room facilities to ensure structural integrity, fire safety, and public health. Compliance with building codes may include requirements for structural design, insulation materials, fire-rated construction, ventilation systems, and emergency egress. Cold room operators should consult local building authorities and regulatory agencies to determine applicable building codes and ensure compliance with all requirements.
- Environmental regulations: Environmental regulations govern the use and disposal of refrigerants, chemicals, and waste materials associated with cold room operations. Compliance with environmental regulations may include requirements for refrigerant leak detection, containment, reporting, and proper handling and disposal of hazardous substances. Cold room operators should implement environmentally responsible practices and procedures to minimise environmental impact and ensure compliance with regulatory requirements.
- Health and safety requirements: Health and safety regulations establish requirements for workplace safety, employee training, personal protective equipment (PPE), and emergency preparedness in cold room environments. Compliance with health and safety regulations may include requirements for temperature monitoring, emergency lighting, first aid provisions, and employee training on safe handling practices and emergency procedures. Cold room operators should prioritise their employees' and visitors' health and safety by implementing robust safety programs and adhering to all applicable regulations and standards.
Note: By adhering to building codes, environmental regulations, and health and safety requirements, cold room operators can mitigate risks, protect public health and safety, and demonstrate their dedication to legal and ethical business practices.
Let professionals help with the material selection
The construction of a cold room requires careful consideration of various materials, components, and factors to ensure optimal performance, energy efficiency, and regulatory compliance.
The professional installation of these materials is critical, from planning and designing the cold room layout to selecting appropriate structural materials, insulation, refrigeration system components, doors, lighting, and monitoring systems. You should make it a point of duty to contact only these people for their help and expertise.